Process Map
When using a new alloy or a new type of powder, the program allows you to quickly create a process map by varying the speed, power, and width of the laser beam over a wide values range. Such calculations take only a few hours. As a result, you will obtain the depth of melting, the width and uniformity of the tracks, and you will be able to start printing parts within the selected range of parameters.
Tiny part morphology
When constructing small thin structures such as walls, bridges, and sharp corners, it is important to understand the surface structure and the quality of powder fusion. On overhanging parts of a detail, material hanging drips can form, and unfused powder may accumulate in cavities. Material overflows can also occur at the turning point of the laser beam. Simulation can be used to analyze scanning strategies when building small details to avoid undesirable phenomena.
Meltpool dynamics
The program uses a hydrodynamic model with a free surface, which allows simulating the behavior of the melt in the melt pool during the printing process. The model takes into account all important hydrodynamic effects: viscosity, surface tension and wettability, thermal conductivity, Marangoni convection, recoil pressure and evaporation from the surface, and convective cooling. As a result of the calculation, the user can see and analyze the fluid dynamics in the melt pool, the shape of the well, temperature distribution and gradients, as well as the quantity and size of ejected droplets.
Total absorbed energy
Information about the total absorbed energy is one of the most important factors when selecting the parameters of the energy source. Depending on the dynamics of the melt pool, the amount of beam reflections inside the well changes, as well as the angle of incidence of radiation on the melt surface. As a result, the total absorbed power dynamically changes during the part construction process. Through mesoscopic modeling, the total absorbed power can be predicted. This prediction can be used to assess the necessary power input in different parts of manufactured detail.
Variation of alloy components concentration
During the layer-by-layer construction of a part, individual areas of it undergo multiple remelting. Due to the dynamics of the alloy in the melt pool, individual components of the alloy mix and come to the surface, where evaporation occurs. Since the evaporation temperature for different components of the alloy may vary, their concentration in the final part will differ from the concentration in the initial powder. KiSSAM allows for the consideration of multicomponent evaporation and provides the distribution of the concentration of individual alloy components in the resulting part. This is especially important for alloys whose properties are most sensitive to composition.
Density and porosity
The porosity of the material obtained through selective laser melting is one of the key quality characteristics of the part. Pores can form as a result of lack of fusion of the powder, as well as during the formation and solidification of cavities in the actively changing area of the melt pool (keyhole pores). Both types of pores can be predicted using mesoscopic modeling. The accuracy of the description and the minimum size of the pores are determined by the spatial mesh step. When choosing a mesh step from 3 to 5 microns, all larger pores will be obtained in the modeling.
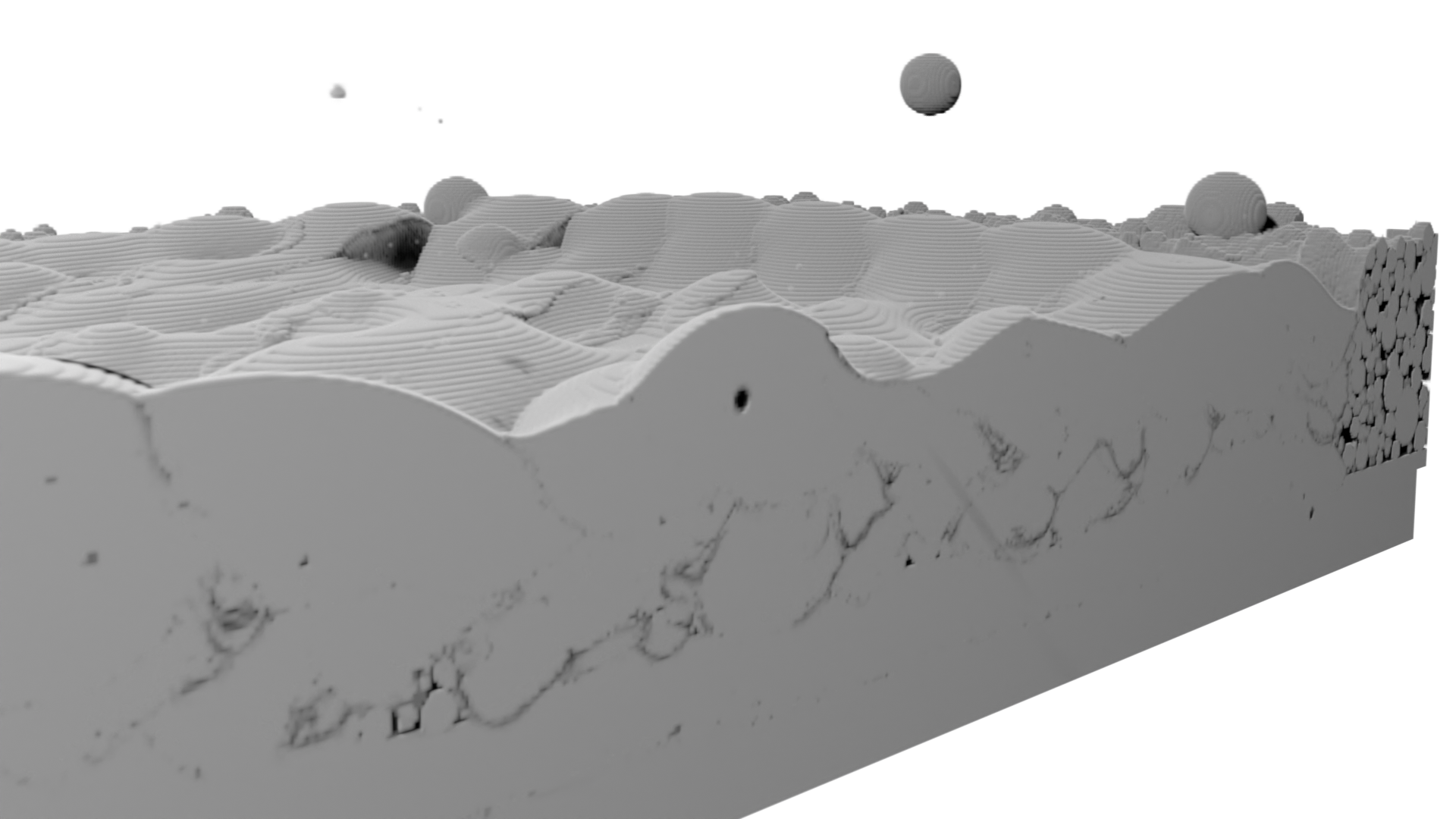
Microstructure
Microstructural features of the material include grain size, grain orientation and their distribution inside the solidified material. The microstructure affects on the presence of defects like porosity or microcracks, as well as the mechanical properties of the material, including strength, ductility, hardness, and fatigue resistance.
Temperature history
During the calculation of powder layer melting, the complete thermal history is stored. The user can create a temperature distribution map at any time step, or place temperature sensors at any chosen points. When constructing a multilayer part, the temperature in the area under the laser (or electron beam) increases and decreases repeatedly. This can affect the microstructure of the part, the final composition of the alloy, and the residual stresses. The obtained values of the temperature fields can be used to analyze the strength and other properties of the material at higher levels of modeling.